Established in the 19th century, the Iittala glass factory is the largest in the Nordics and the only one left in Finland. Design Stories got to take a tour of the glassworks to see how Aalto vases, Leimu lamps, and Ultima Thule glasses are made. Come along!
FLAGS WITH THE FAMILIAR i LOGO flutter about next to the parking lot as we arrive at the Iittala glass factory in the Finnish village of the same name. We are in for a treat, as our plan for the day is to watch Iittala’s glassblowers turn hot, molten glass into mind-bending art glass as well as elevating everyday tableware.
You may already know that the iconic i logo was designed by the renowned Finnish artist and designer Timo Sarpaneva, but do you know what it symbolizes, besides the letter I? If not, find out at the end of the story!
The only one in Finland
The Iittala glass factory was founded in 1881, and it is nowadays the largest in the Nordics – and the only one still active in Finland. This is where Iittala's glassblowers craft iconic vases by Alvar Aalto, playful glass birds by Oiva Toikka, and the uniquely ice-like Ultima Thule glasses by Tapio Wirkkala. We are told the factory employs around 200 people, around 60 of which are glassblowers. Other glass professionals include quality controllers, polishers, engravers, and packers, to name a few.
Alongside hand-blown artifacts, the factory also produces utility glass on machine lines, either by pressing or with the centrifuge method. In the latter, molten glass is cast into a spinning mold, which forces the glass to spread evenly inside it. We didn’t think we’d learn physics today, but we’ll take it! This method is used to make the Ultima Thule bowls and Kastehelmi serving platters, for example.
Years of practice
After our physics class, we get to learn some chemistry, as we hear about how glass itself is made. The recipe contains ingredients like Belgian sand, soda, and calcium carbonate, which are molten into a red-hot, honey-like mass in the factory’s massive furnace called Vihtori (the machine line is called Vesa).
The glassblowers responsible for blowing the Aalto vases have trained in the craft for at least five years.
Glassblowing is far from easy – it shows true artisanship and requires years of training. For example, the glassblowers responsible for blowing the Aalto vases have trained in the craft for at least five years. An equally challenging object is the Ruutu vase by Ronan and Erwan Bouroullec, and both pieces require as many as seven professionals, 12 work steps, and up to 30 hours of work depending on the vase’s size. The most time-consuming step is annealing or cooling, which removes tensions from the mass and allows the colors to develop.
And in case you’re wondering: Tapio Wirkkala’s Kantarelli is apparently the trickiest to make. We are told that only a few glassblowers can do it.
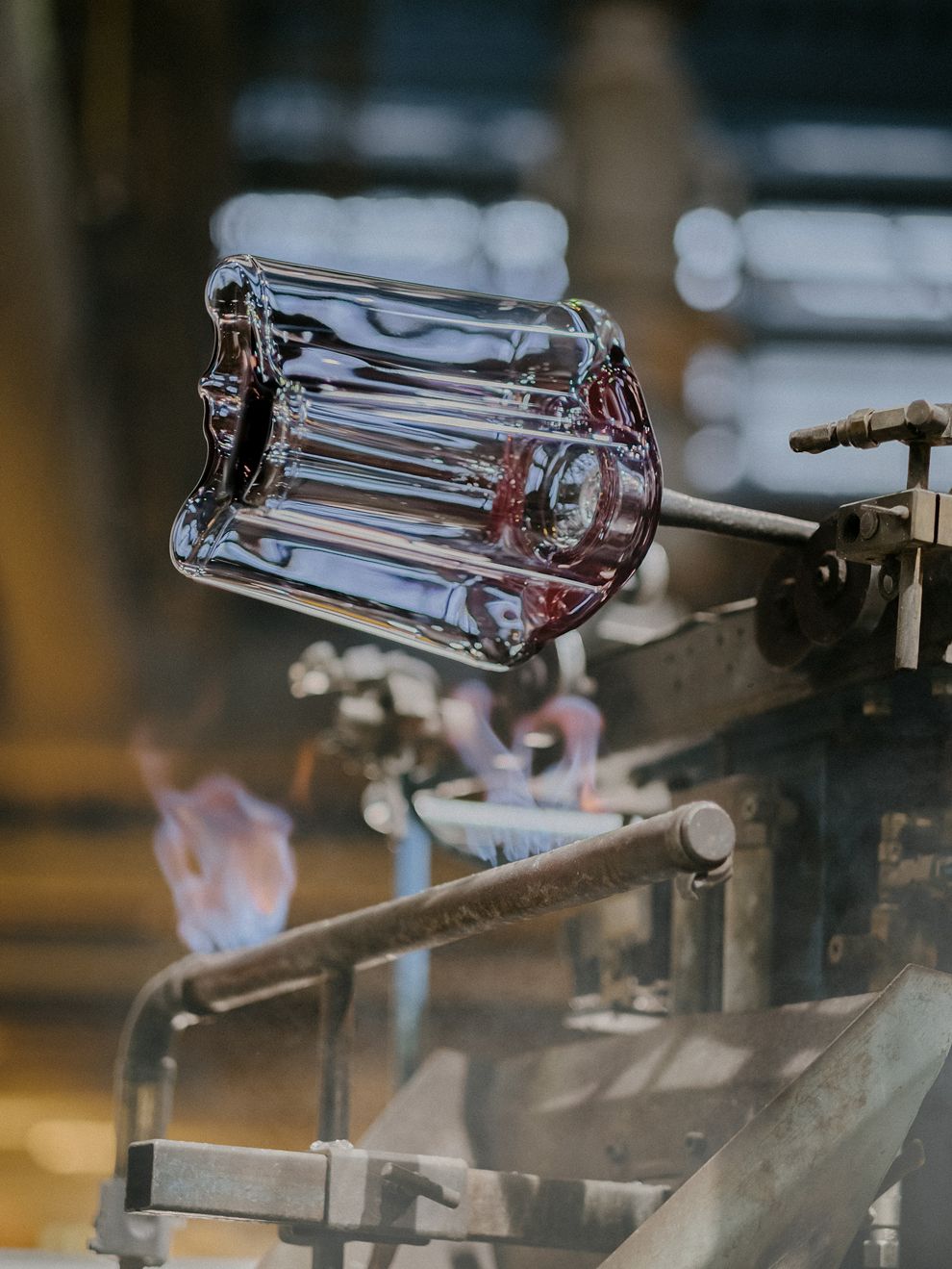
Expert in colored glass
As Finns, we have been using Iittala’s items since we were kids, so never even realized that colored glass was something extraordinary. We’re so used to cranberry-red Aalto vases and rain-blue Kastehelmi candleholders that we have always taken it for granted that the color never fades or rubs off.
Iittala’s colored glass is made by adding various oxides to the glass recipe.
Iittala’s colored glass is made by adding various oxides to the glass recipe. We hear that brown and red glass is made with copper oxide, while blue is made with cobalt. Creating a new color recipe may take years, and yet, Iittala’s color archive consists of over 200 of them. Around 20 glass colors are usually in production at a time.
Against throwaway culture
At the end of our visit, we hear about the factory’s recent strives in sustainability, recycling, as well as health and safety. At the beginning of October 2022, Iittala’s parent company Fiskars announced that the glass factory’s furnaces will be renewed and updated to ones that run on renewable energy, which will significantly reduce the entire factory’s emissions and energy consumption.
Recycling has also been a hot topic in recent years at the factory, and since 2016, none of the production lines’ scrap glass has gone to waste. Some of it is used for making new products and the rest is recycled in other ways. Not all waste glass is suitable for reuse at the factory, so it is transported elsewhere for repurposing and used to make glass wool, for example. So, in theory, our homes or office buildings could be insulated with pieces of Aalto vases or Kastehelmi candleholders!
With this amusing thought lingering in our heads, we wave goodbye to the factory and the red-and-white i flags waving in the wind. Oh, and the meaning of the logo: the lowercase i symbolizes a blowing pipe with a bubble of glass at the end, surrounded by the flaming red mouth of a furnace.
Iittala favorites
See also:
• Iittala products at Finnish Design Shop >
• Preloved Iittala products at Franckly >
Text: Emmi Ratilainen Images: Iittala