The elegant, tradition-inspired Biennale stool takes at least 12 weeks to make, requiring not only skill but also quite a lot of physical strength from Nikari’s cabinetmakers. Read on to find out how exactly the stool is made!
NOT MANY DESIGNS have caused as much of a stir in recent years as Nikari’s wooden Biennale stool. Designed by Nikari’s founder Kari Virtanen, the stool was initially created for the Finnish pavilion of the 2014 Venice Architecture Biennale, where it represented a modern, elegant version of a traditional log stool that you may see at Finnish summer cottages or around a campfire.
But how does the designer stool differ from its rustic, often self-made counterpart? Design Stories asked Nikari's CEO, Johanna Vuorio, how exactly is the stool crafted.
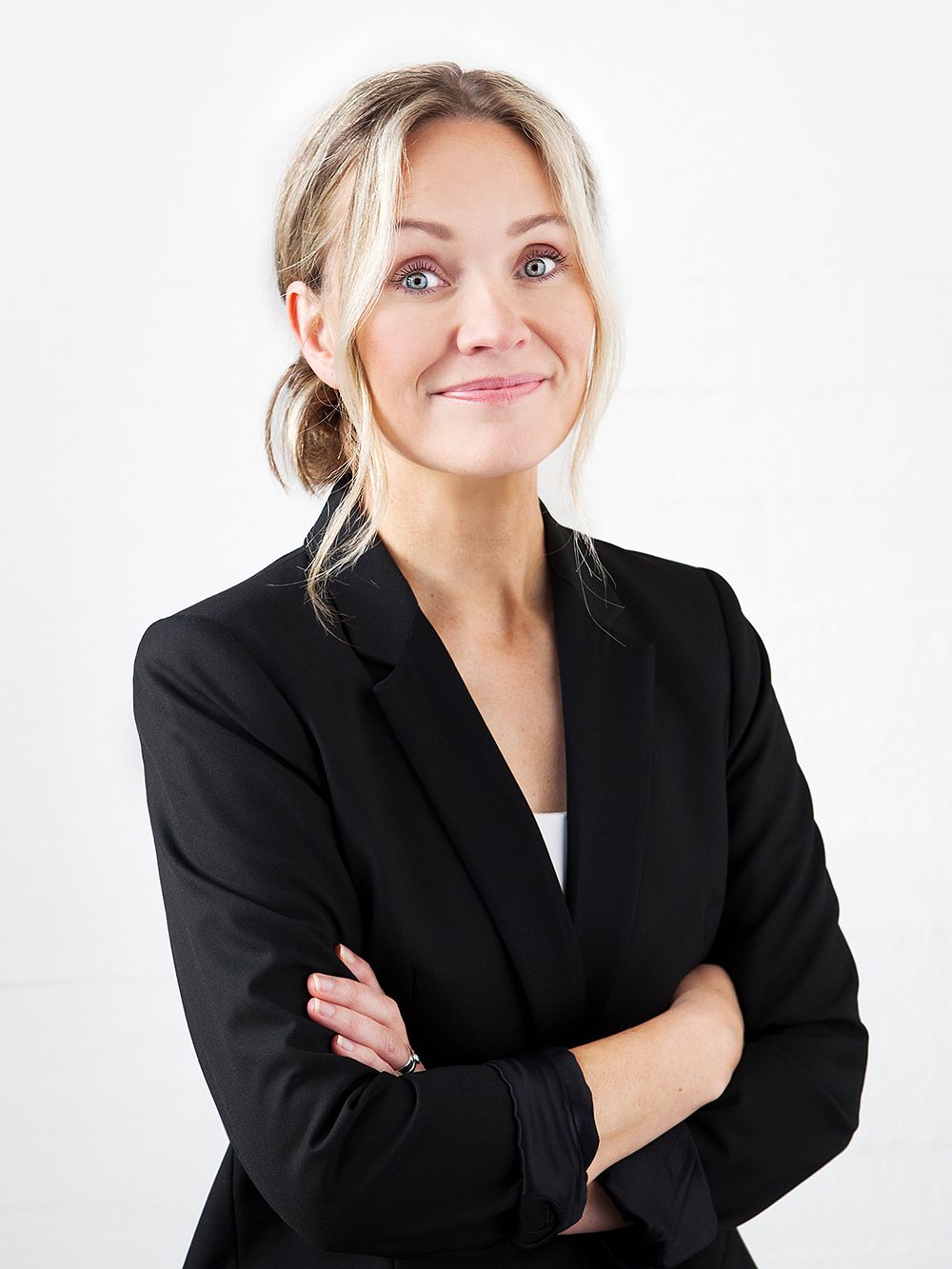
Simple and streamlined
Biennale is a prime example of a typical Nikari piece in that it combines a modern design language with traditional artisan techniques. Although drawing inspiration from a very traditional piece of furniture, Kari Virtanen gave the stool a streamlined, rectangular form that creates a lovely contrast to the log stool’s more rustic look.
Do not let the simple form of Biennale fool you though – its production process is far from simple.
“It requires both skill and physical strength to make the stool,” says Johanna Vuorio, who has been Nikari’s CEO since 2010.
In addition, it also requires quite a lot of time: if you count each and every step – from sawing and transportation to finishing – the process takes at least 12 weeks, and often longer still.
“Drying the wood takes the most time,” says Vuorio. “It must be done properly so that the massive chunk of wood won’t crack or even shatter. It often takes twice longer than planned!”
• Read also: Kari Virtanen, cabinetmaker and founder of Nikari, wins the Kaj Franck Design Prize 2022 >
Show of skill and strength
When the wood block is finally dry, it still takes several steps to get to the finished product. After surface planing to perfect the rectangular shape, sawing the block to the desired size, and sanding the surface smooth, the stool needs to be cross-sanded to obtain a lovely matte texture – not to mention all the finishing touches.
All corners and the edges of the characterful cracks must be smoothed to prevent splinters, and then the entire object finish-sanded before applying a natural wood oil mix. The latter is even done twice with the stool sanded yet again between the oil mix layers.
“Due to the physical strain of the work, one cabinetmaker can only craft a limited number of stools per week.”
“The steps following the drying are quicker in theory, but they require a lot of physical strength from the artisan,” says Vuorio.
“The block weighs a lot, and it takes a while to buff out all the sharp edges. Due to the physical strain of the work, one cabinetmaker can only craft a limited number of stools per week.”
High quality equals long life
Also typically for Nikari, Biennale’s design and production are based on sustainability: the blocks come from parts of oak logs that would otherwise be unused due to, for example, a lighter shade of wood, branches, or the cracks that give Biennale its unique character.
“Making sawn timber from them would be largely unprofitable and difficult," explains Johanna Vuorio. "This has been the idea behind the product from the start: that this surplus material would also find use, and that it would not end up, for example, being just burned."
However, the quality of the wood material must be top class, and rot damage, for example, is not allowed. The quality requirements are also strict for the cracks so that the stool is sure to last from one generation to the next.
"Because of wood's carbon sink property, it is valuable to produce products that are further processed and last for centuries. In all its simplicity, the Biennale is exactly that – it remains a carbon sink as long as it is not burned or decomposed."
See also:
• Biennale stool >
• All products by Nikari >
Text: Emmi Ratilainen Images: Mira Ahola, Niclas Mäkelä and Nikari